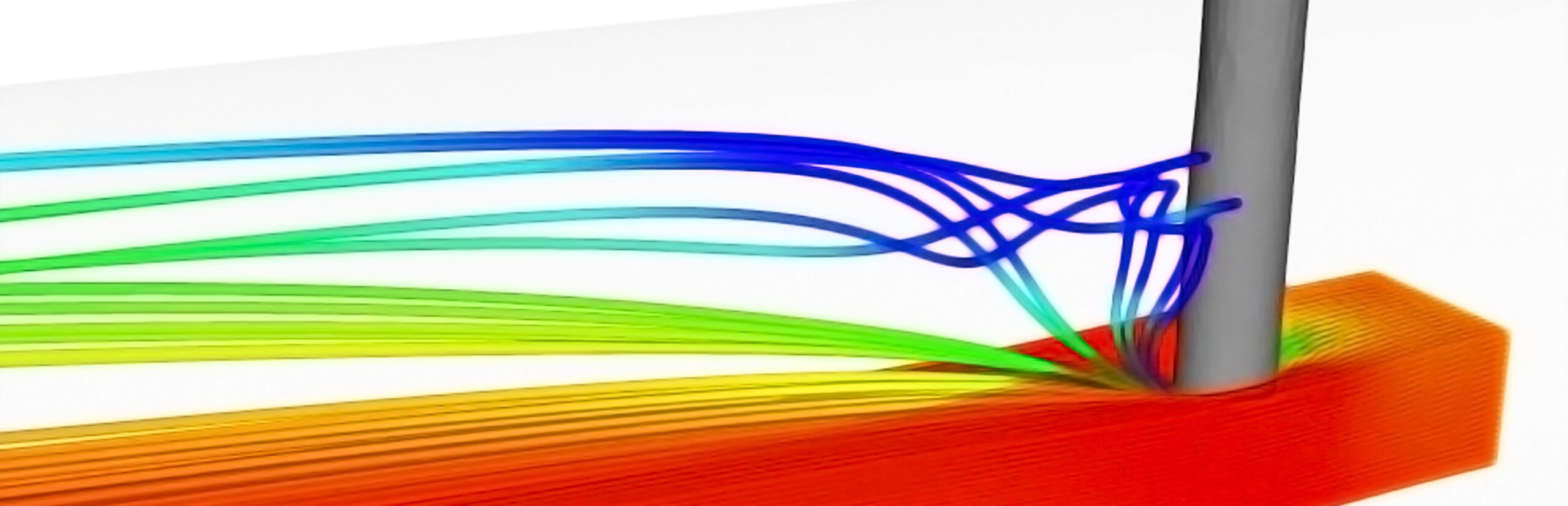
Project Case Study
News ⋅ Project Case Study: Consultancy Services & CFD Modelling
Consultancy Services & CFD Modelling
ECI Group provides specialist services at all stages of plant lifecycle. An LDPE plant operating company recently reached out to us after experiencing corrosion problems close to one of the peroxide injection points on their reactor. ECI Group’s experienced engineers examined the overall system, then performed a formal root cause analysis to investigate the problem and identified solutions for our client.
The Project
A client operating a tubular homopolymer plant recently discovered localised corrosion in the tubes downstream of the peroxide injection point which required a number of shutdowns and tube replacements to continue safely running the plant.
The client approached ECI Group, and our experienced plant troubleshooting team performed an initial diagnosis of the potential likely causes. Subsequently, the client requested a formal Root Cause Analysis and a Computational Fluid Dynamics modelling study of the peroxide injector.
ECI Group identified and examined a number of potential root causes and focused on the most likely identified causes: the quality of the peroxide and the peroxide dispersion. These root causes were investigated in detail and CFD modelling confirmed that a small build-up of polymer could develop on the quill during certain flow conditions. This prevented the quill from adequately dispersing the peroxide and encouraged the peroxide to impinge and pool on the inner surface of the high-pressure tubing, causing corrosion. This was made worse by the presence of reactive species in the peroxide, which had been insufficiently neutralized by the peroxide suppliers.
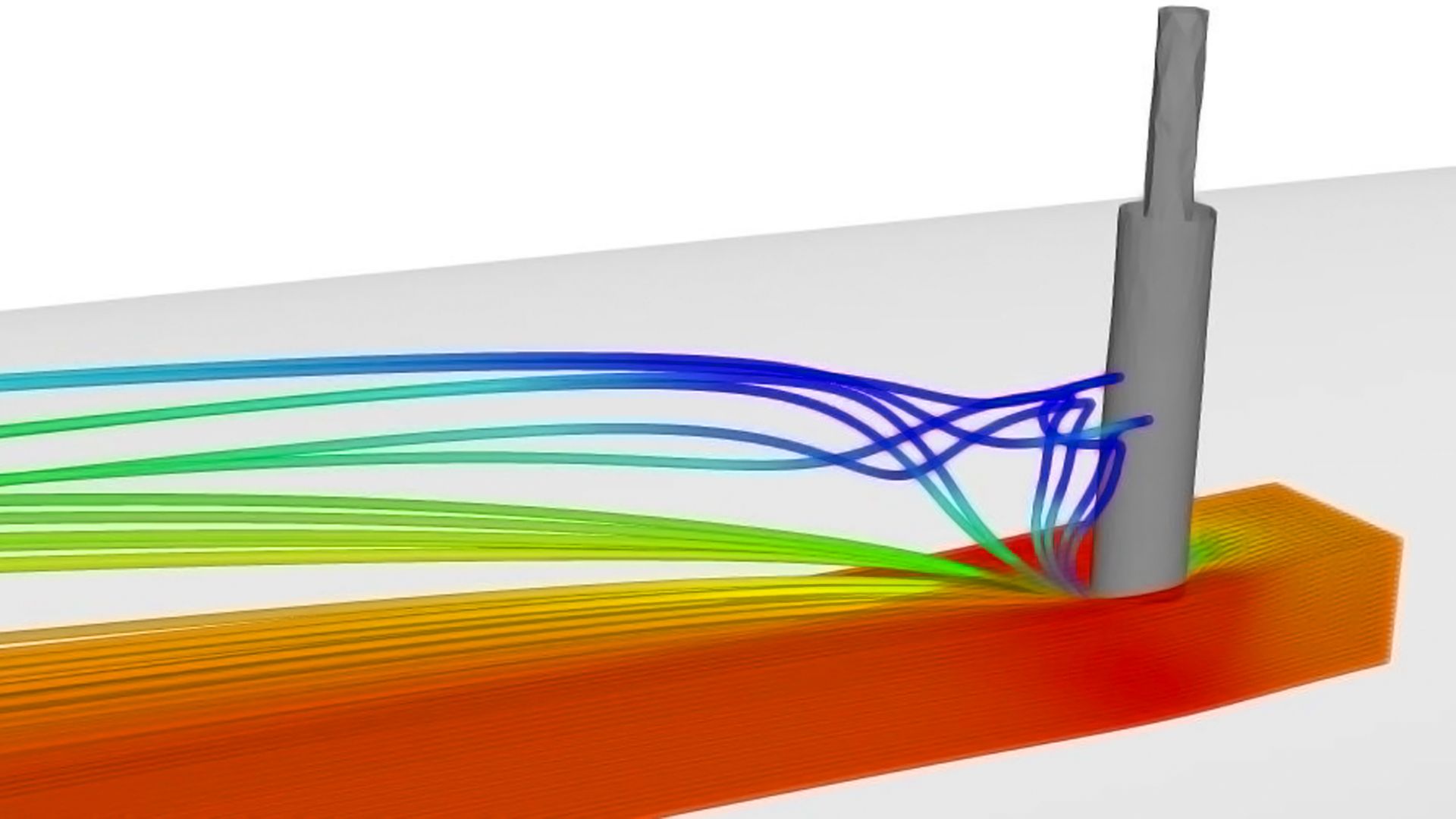
ECI Group’s Recommendations
ECI Group recommended a re-design of the peroxide injection quill and optimisation of the injection lens ring design. We also advised that the peroxide specifications were tightened to prevent the recurrence of reactive species, and that solvent flushing during or after the reactor shut down should be implemented.
If you are experiencing problems with your polymer plant, or believe it is not performing at its optimal level, then contact us today to see how our engineering experts can provide a solution. Regardless of the plant’s original license or design, ECI Group’s subject matter experts can help.