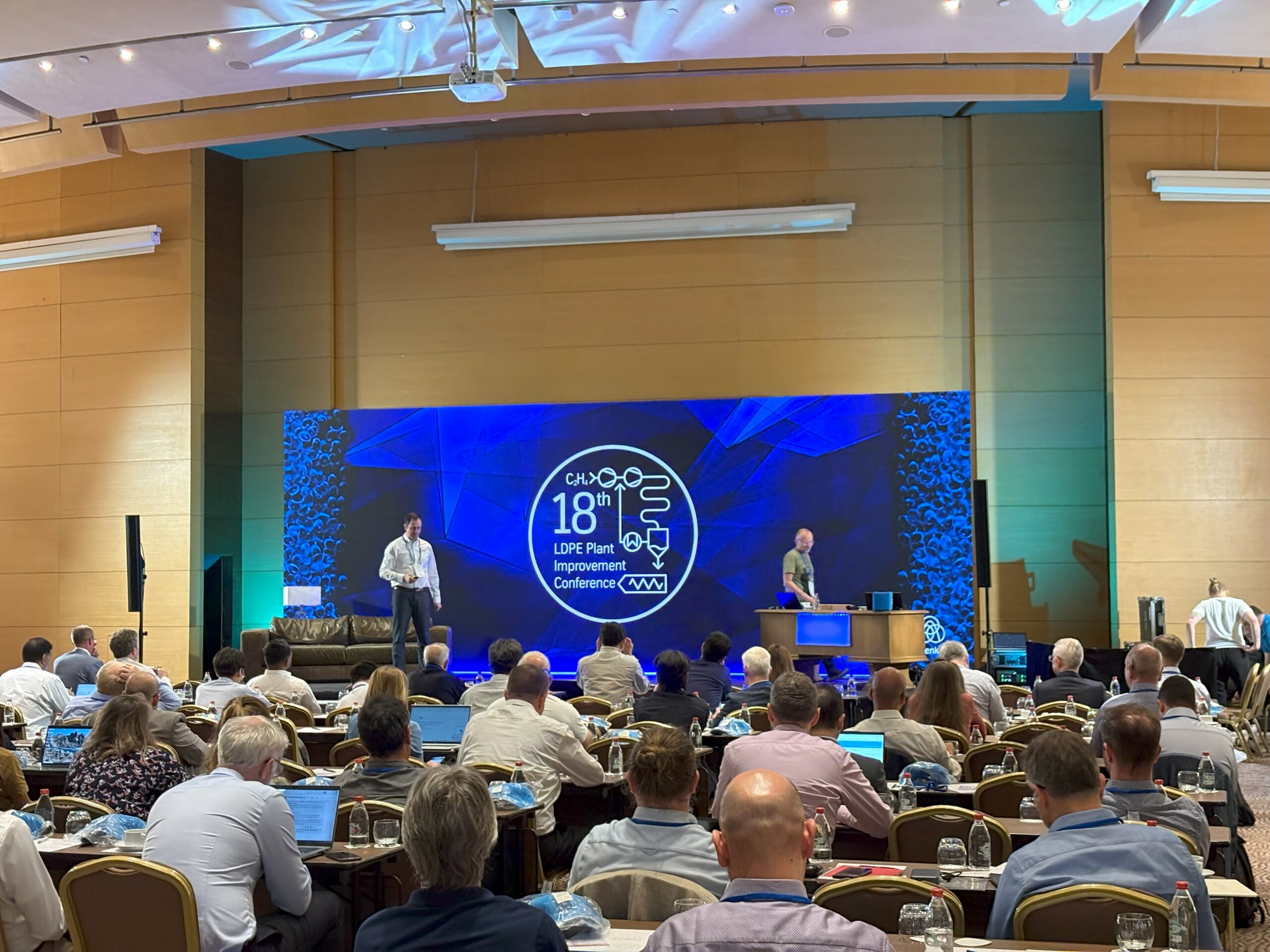
18th LDPE Plant Improvement Conference
News ⋅ 18th LDPE Plant Improvement Conference
Highlights from the 18th LDPE Plant Improvement Conference
2nd – 3rd June 2025, Izmir, Türkiye
ECI Group was proud to be a Platinum Sponsor of the 18th LDPE Plant Improvement Conference, hosted by Uhde High Pressure Technologies.
Held in the vibrant city of Izmir, Türkiye, the event brought together nearly 200 LDPE plant operators, equipment manufacturers, and service providers from around the globe.
This annual gathering continues to be a cornerstone for sharing insights, addressing challenges, and showcasing innovations in the operation, maintenance, and enhancement of high-pressure LDPE and EVA plants.
Driving Innovation: Key Themes and Presentations
This year, the conference featured a diverse range of technical presentations across 2 days, covering: safety-focused decomposition and relief processes; market trends and predictive analysis; advanced modelling for optimal plant performance; best practices in cutting-edge equipment and operations.
These sessions fostered open dialogue and knowledge exchange, reinforcing the industry’s commitment to continuous improvement and operational excellence.
Burckhardt Compression’s LDPE Technology Day followed the conference on June 4th, providing informative discussions and knowledge exchange on optimizing compressor performance on LDPE & EVA Plants.
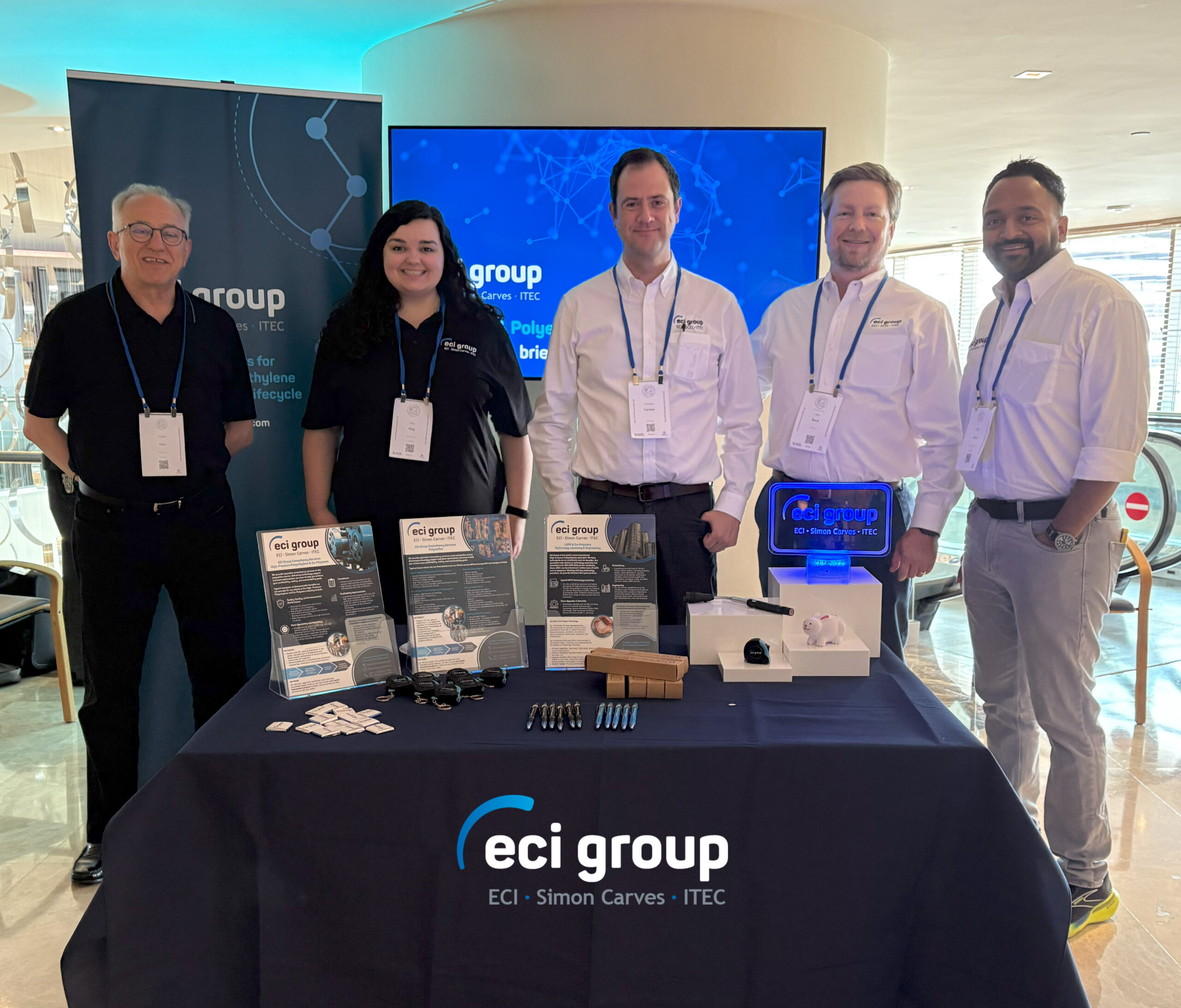

Introducing the ECI Group SuperCooler™
A major highlight was the unveiling of the ECI Group SuperCooler™, presented by ECI Group’s Vice President and HPPE Division Director, Chris Brock.
In his talk, ‘The evolution of modularization: introducing the ECI Group SuperCooler™’, Chris introduced the next big leap in ECI Group’s high-pressure technology offering.
The ECI Group SuperCooler™ will offer significant plant improvements, including:
- Reduced pressure drop
- Increased annual heat transfer effectiveness
- Reduced ethylene inventory and reduced reactor bay footprint
- Significant capital and operating cost savings
Designed for both new build and retrofit projects, the SuperCooler™ represents the next-generation innovation in high-pressure polyethylene plant performance.
Interested in learning more? Contact us to explore how the SuperCooler™ can transform your operations.
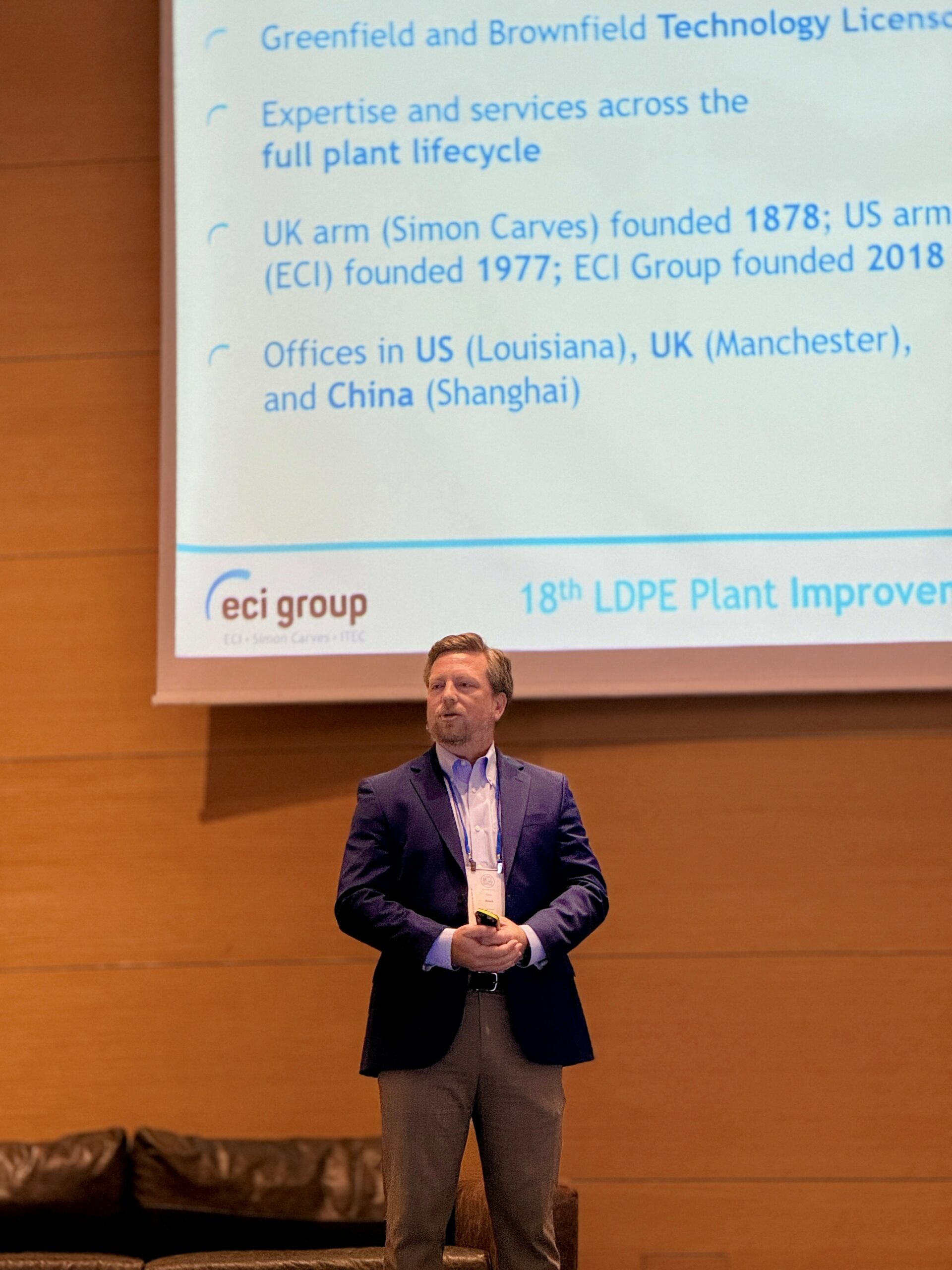
Plant Improvements for LDPE & EVA Operators
On Day 2, Francisco Larenas, ECI Group’s Consultancy Services Director, delivered an insightful presentation on ‘Plant Improvements for LDPE & EVA Operators: Increasing Productivity, Reliability, and Margins.’
The presentation focused on the importance of developing a structured and strategic roadmap to enhance the performance of an operating high-pressure polyethylene plant to a leading competitive position.
Francisco shared a practical example of ECI Group’s Plant Improvement Plan in action, drawing on case studies from multiple facilities to demonstrate a comprehensive path to profitability.
Explore our Consultancy Services, including zero-capital plant improvements, to see how we can support your plant’s journey to peak performance.
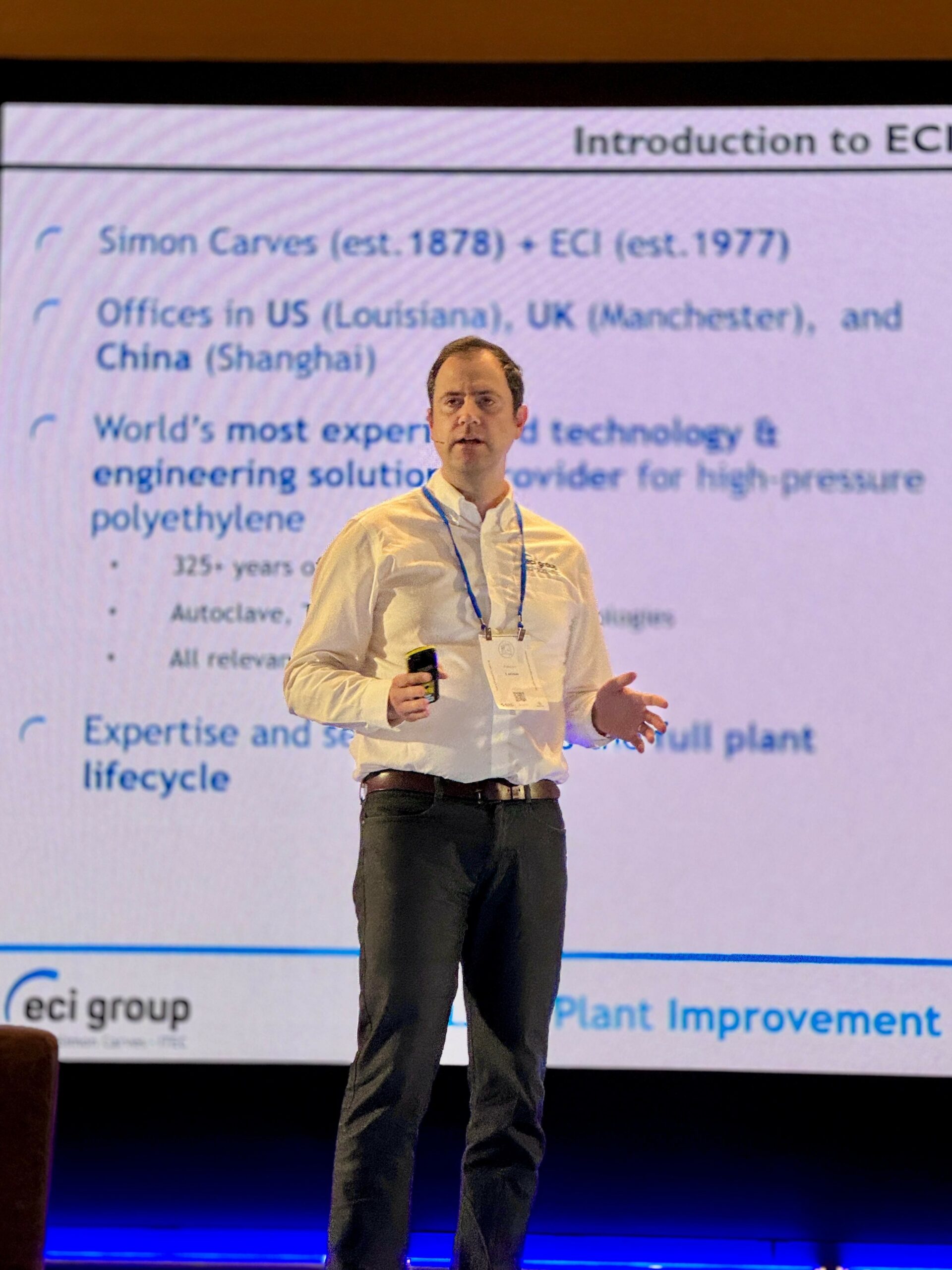
Networking, Culture & Community
Beyond the technical sessions, the conference offered great opportunities for networking and cultural immersion.
Day 1 wrapped up with the annual conference beach volleyball tournament which sparked friendly competition and camaraderie.
Day 2 featured a gala dinner at the historic Agora of Smyrna, where attendees enjoyed traditional Turkish cuisine and a captivating performance of traditional Zeybek dancing.
The event concluded with a scenic sunset dinner at Konak Pier, overlooking the Mediterranean Sea—a perfect end to a memorable conference
-
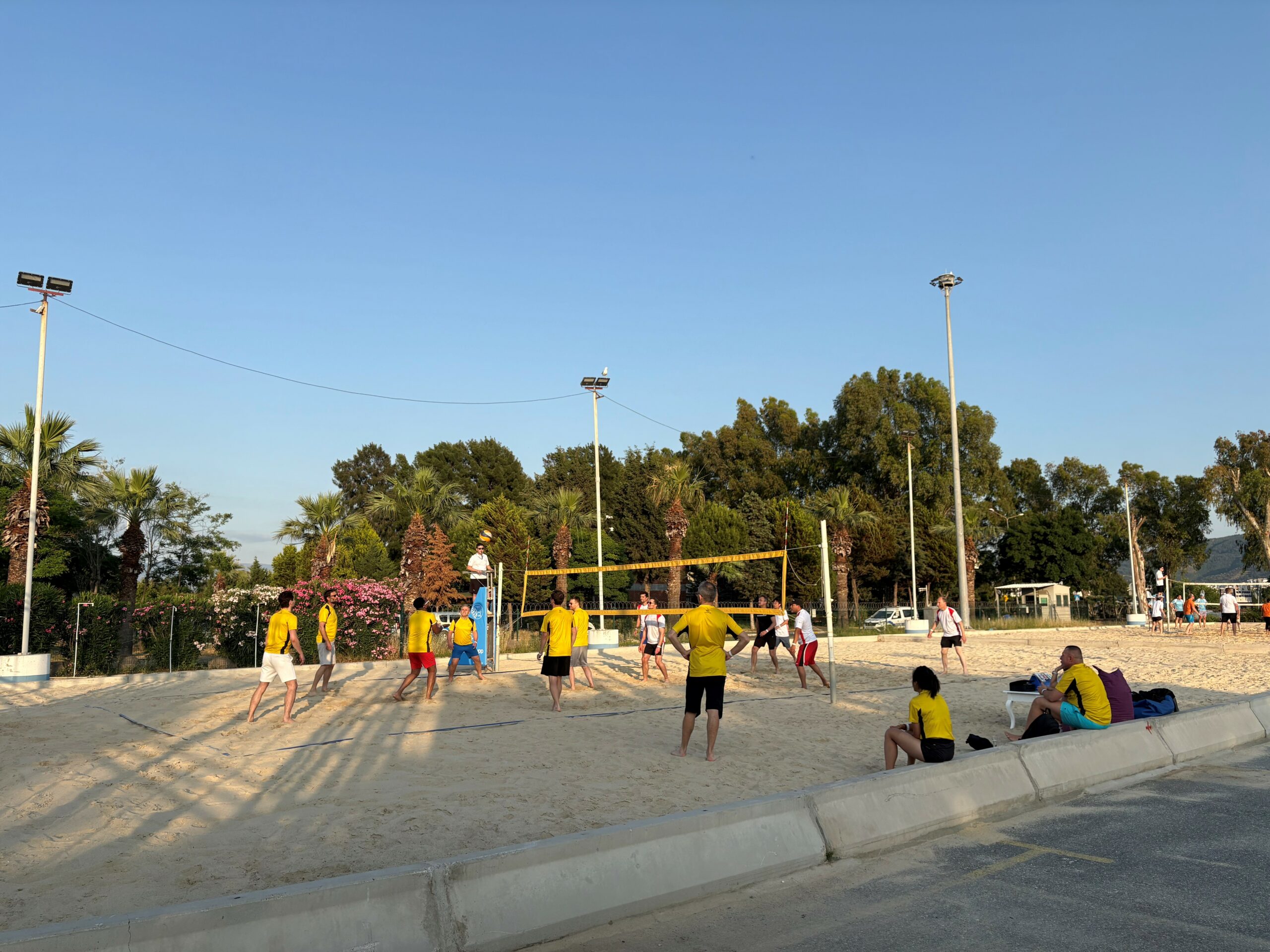
CB LDPE PIC 2025 6
-
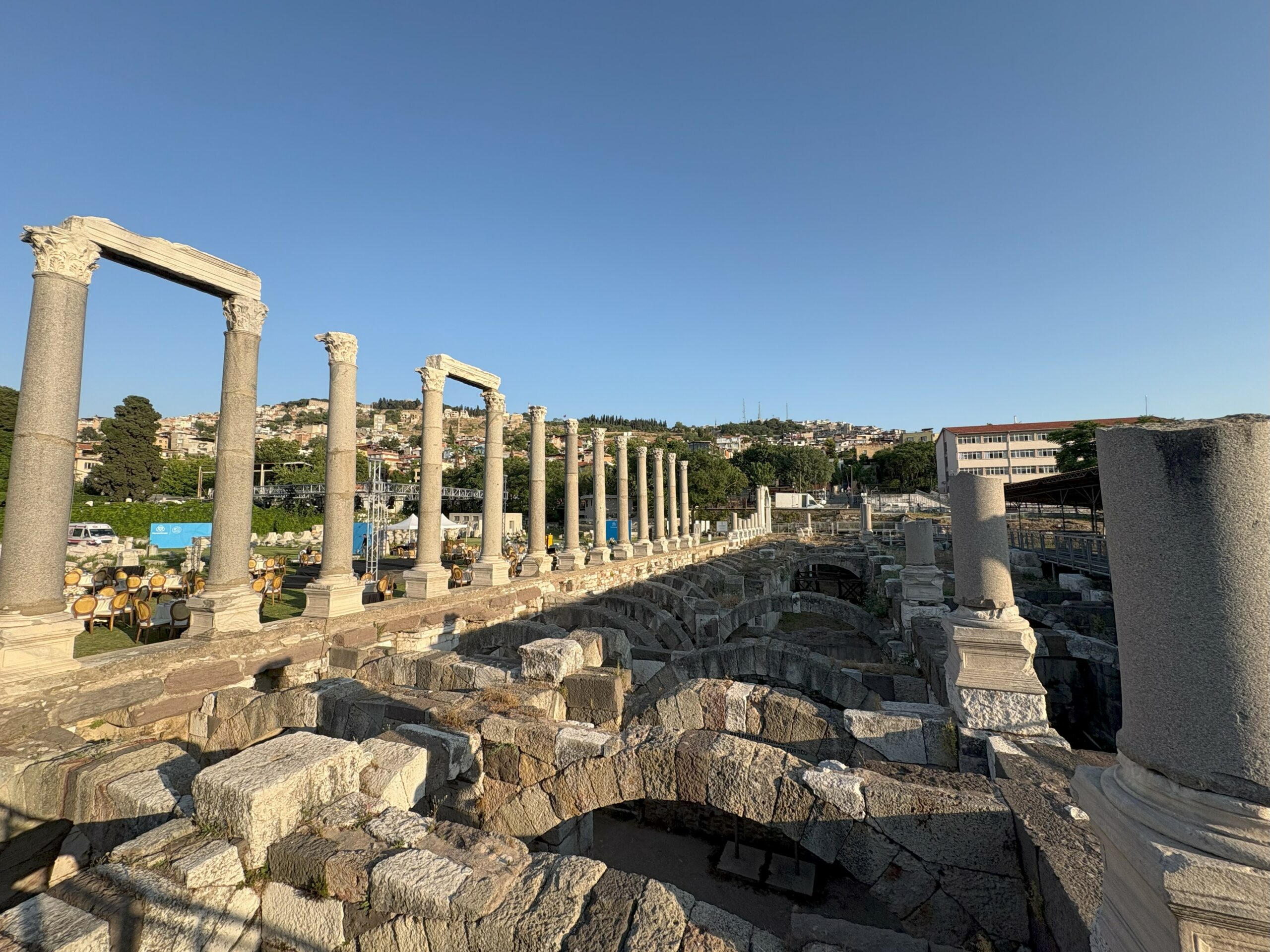
IMG_1646
-
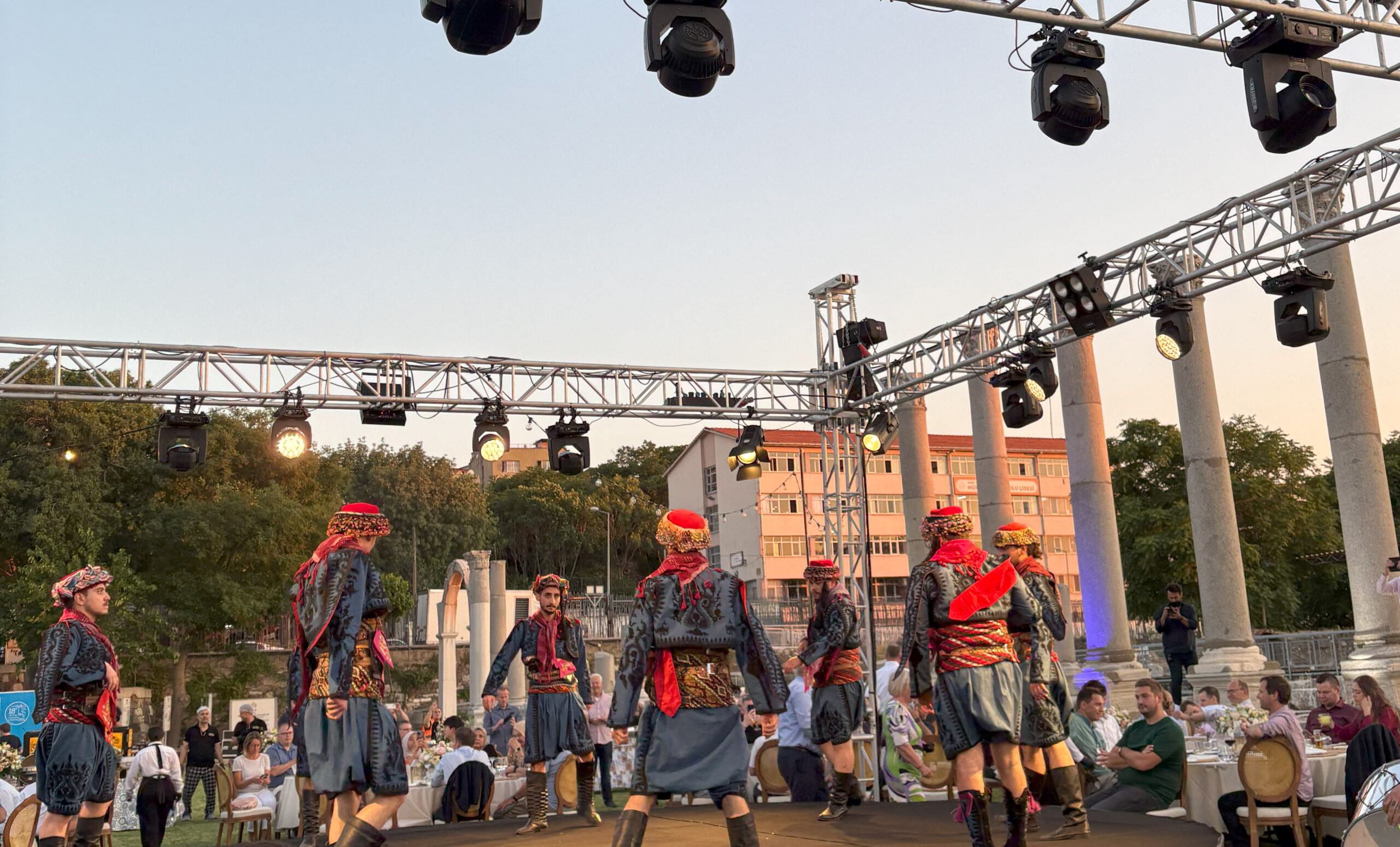
IMG_1654 copy
-
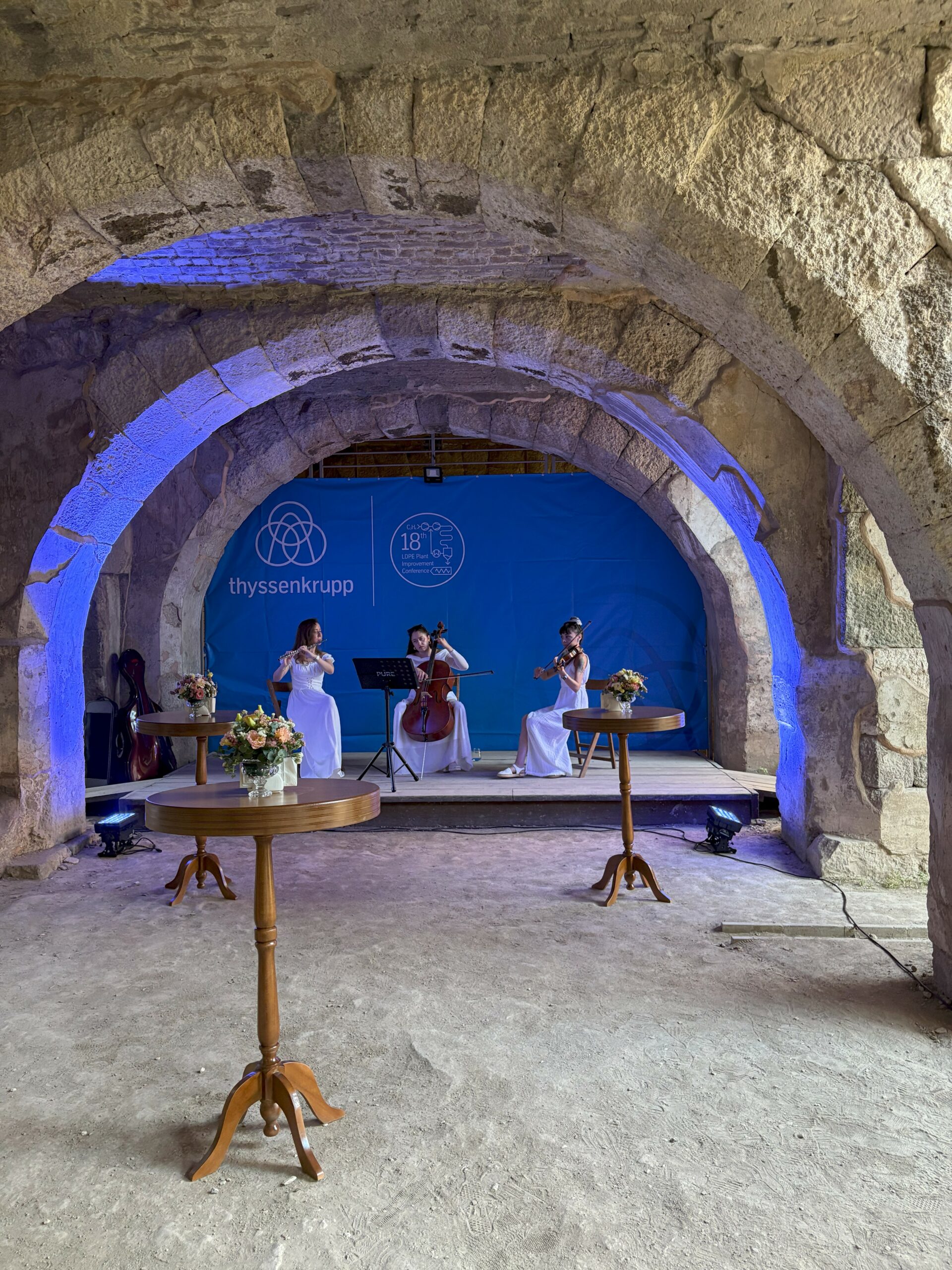
IMG_1627
-
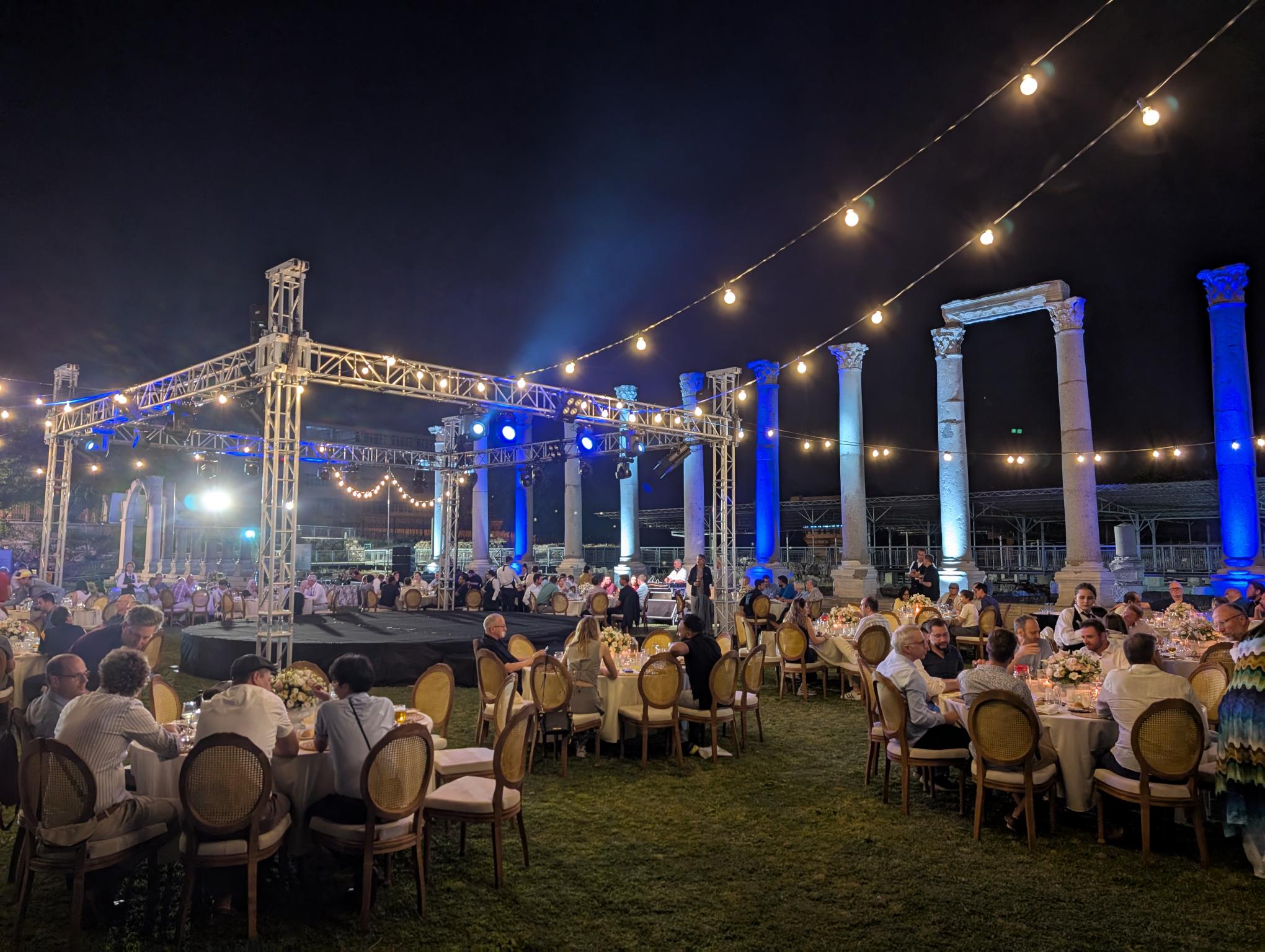
shared image (1)
-
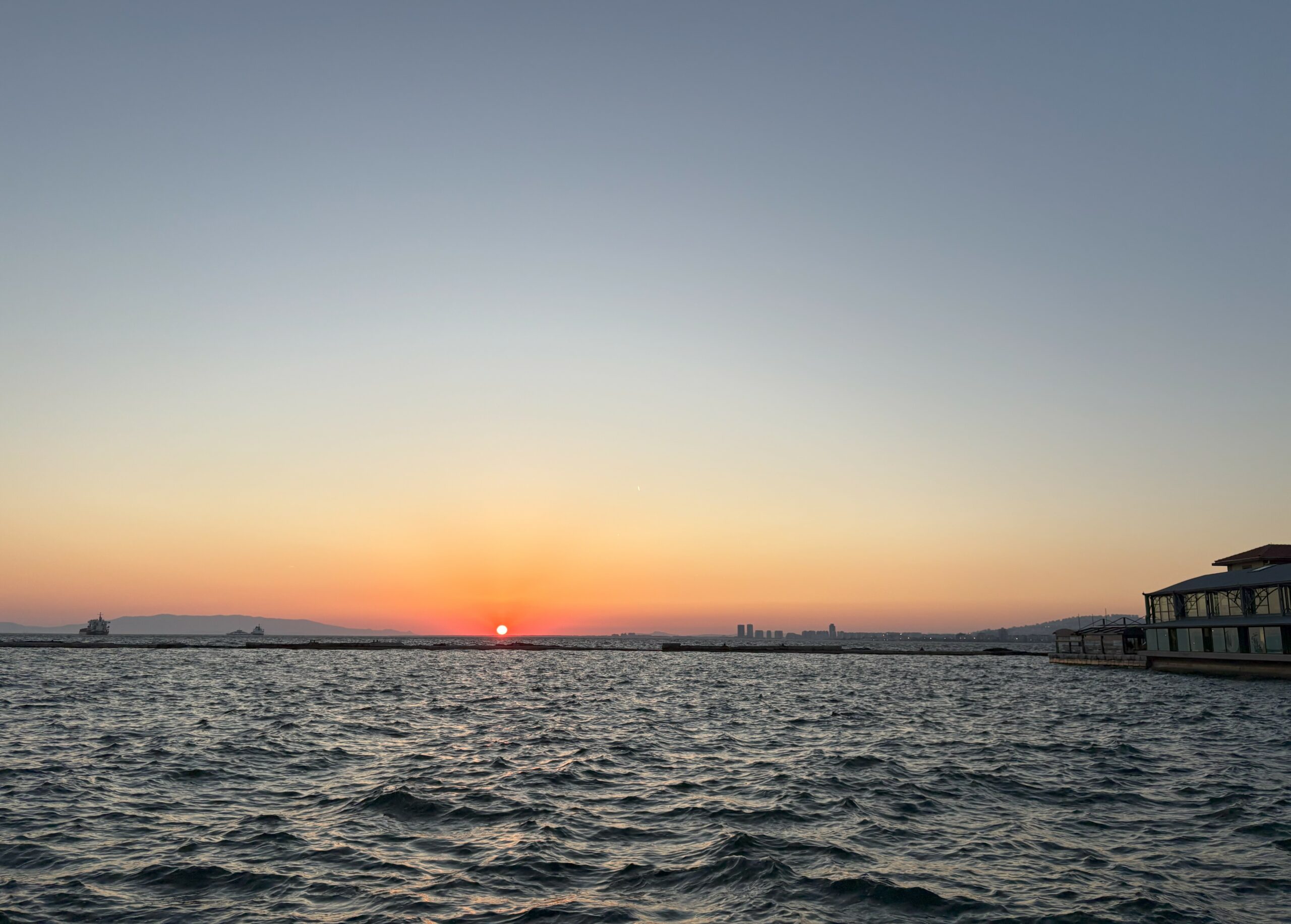
IMG_1646
-
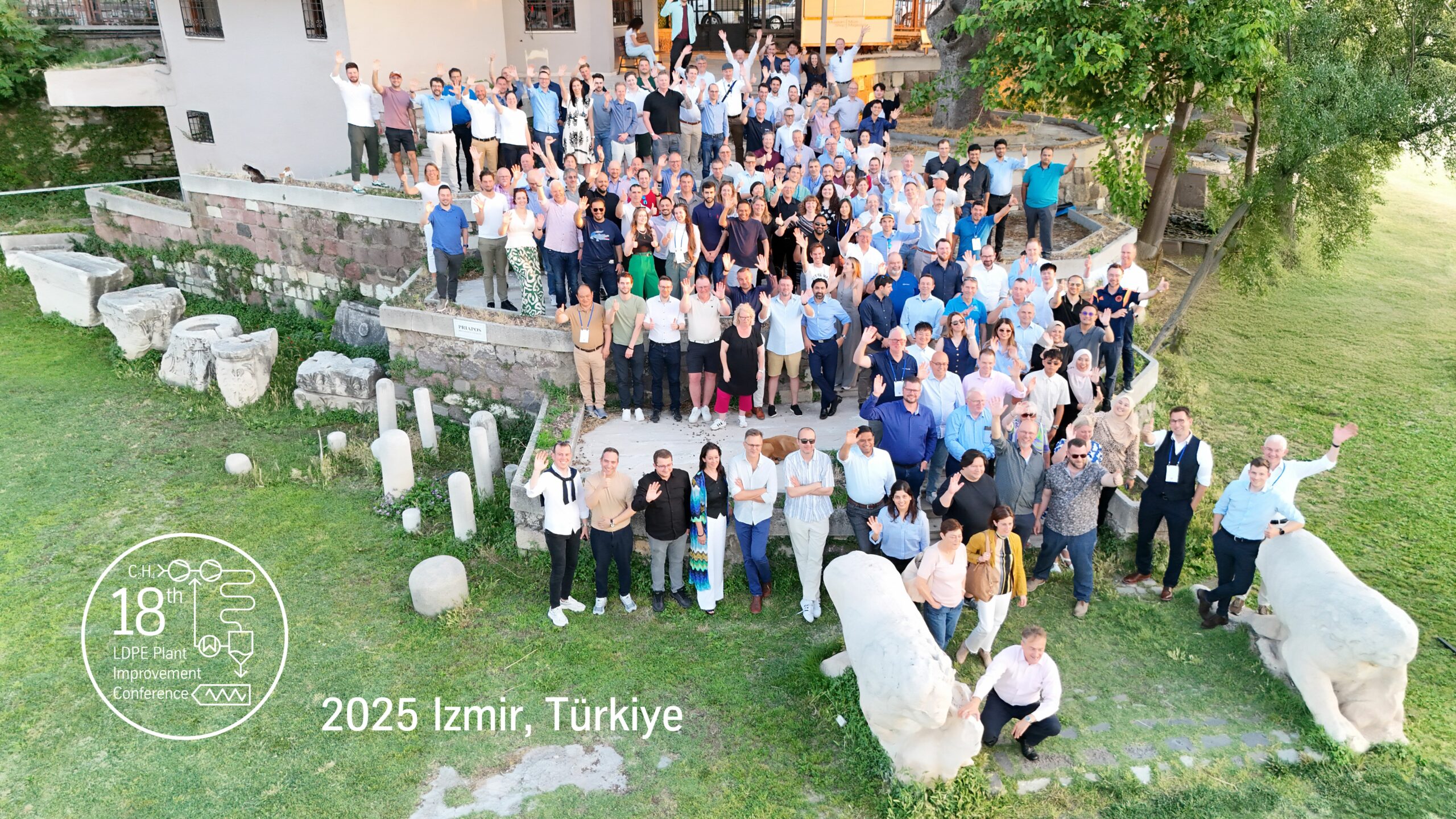
Group Photo
Looking Ahead: Shanghai 2026
The 2025 conference was a resounding success, offering valuable insights and forging stronger industry connections. ECI Group has been a long-term sponsor of the event and we’re already looking forward to the 19th LDPE Plant Improvement Conference, set to take place in Shanghai next year.
We’re going to be working closely with Uhde to deliver expanded technical content for our licensees next year, so watch this space!